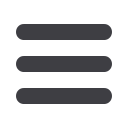
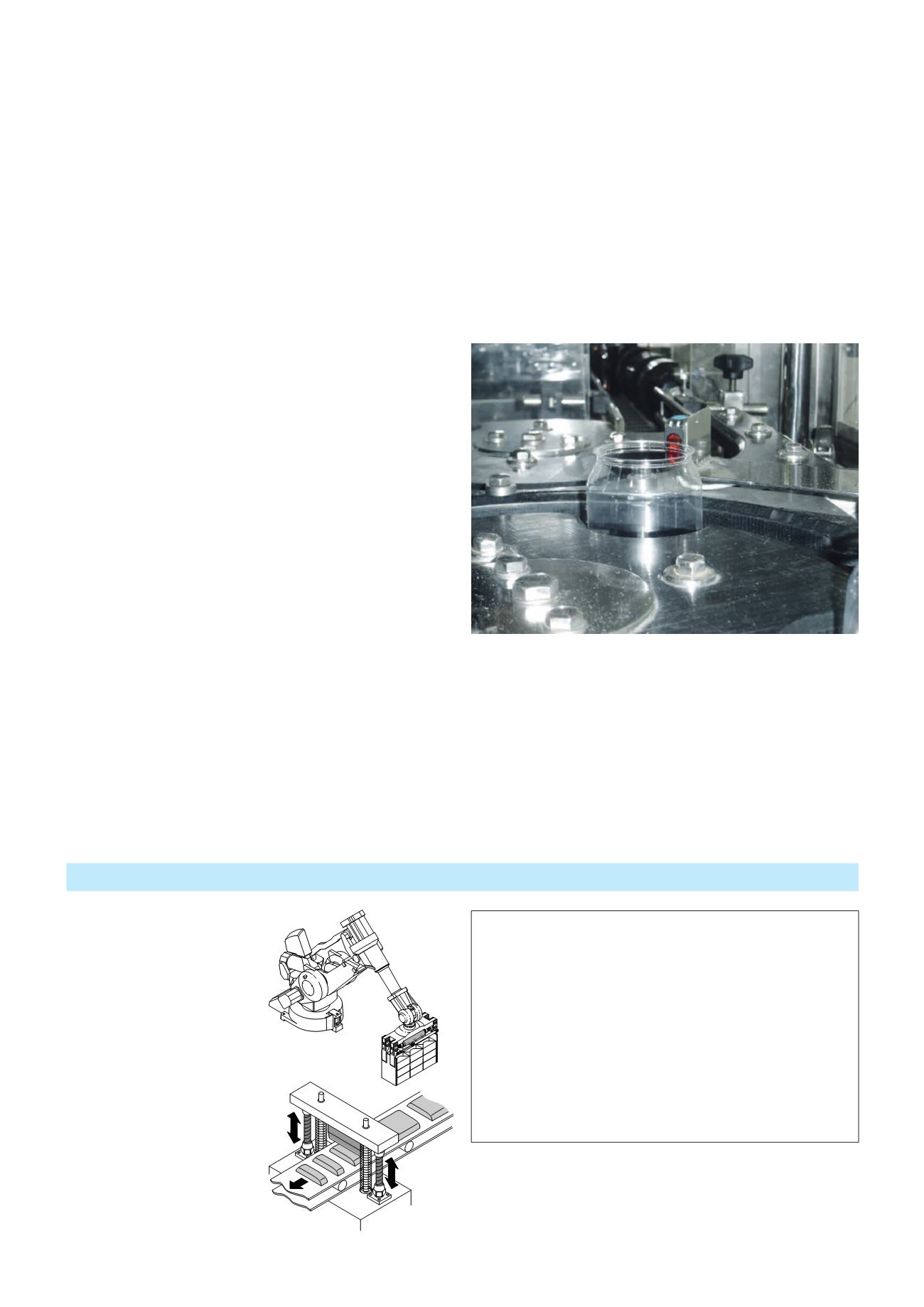
13
2017/11 – Subject to change – Digital simplicity: World first Festo Motion Terminal VTEM
The Festo Motion Terminal can
replace over 50 components
without any problem. This opens
the door for new approaches to
a wide range of applications,
such as an adaptable pneumatic
platform for handling units with
many different grippers. The
Festo Motion Terminal is also
perfectly suited to continuous
processes where the travel time
of the pneumatic actuator is
crucial to process quality and
additional processes can be self-
regulating.
Over 50 components in one valve
18 directional control valves (9 directional control valves in 2 sizes)
8 pressure sensors (ducts 1, 2, 3/5, 4; with 2x 3/2-way valves)
6 pressure regulators (ducts 2, 3/5, 4 with 2 sizes)
5 components for previous Soft Stop applications
4 flow control valves (2x supply air, 2x exhaust air)
3 proportional flow control valves (4/3 and 2x 3/3)
2 proportional pressure regulators
2 shock absorbers
2 external sensors (model-based proportional pressure regulation)
What’s your application?
2. Checking the quality of
containers: simpler, more
cost-effective, more reliable
Motion Apps: Soft Stop
(available Q3/2018),
Proportional pressure regulation
and Leakage diagnostics. In test
set-ups for containers, up to 60
containers per procedure are
tested for stability and leak
tightness.
This requires an even, gentle
application of cylinder force
with a precise level of force
for just a few seconds.
The current solutions comprise
up to 60 motor controllers, the
corresponding sensors, 3/2-way
valves and electric cylinders.
But the Festo Motion Terminal
VTEM can now complete this
task in combination with
pneumatic cylinders DSBC and
position transmitter SDAP.
The effect
Fewer components – greater
reliability. 8 Festo Motion
Terminals replace up to 64
electric cylinders.
The advantages in detail:
• 70% lower costs compared
to an electrical solution
• 65% less installation space
required
• 85% reduction in costs for
wearing parts
• Controlled movement and
leakage detection using the
same components