
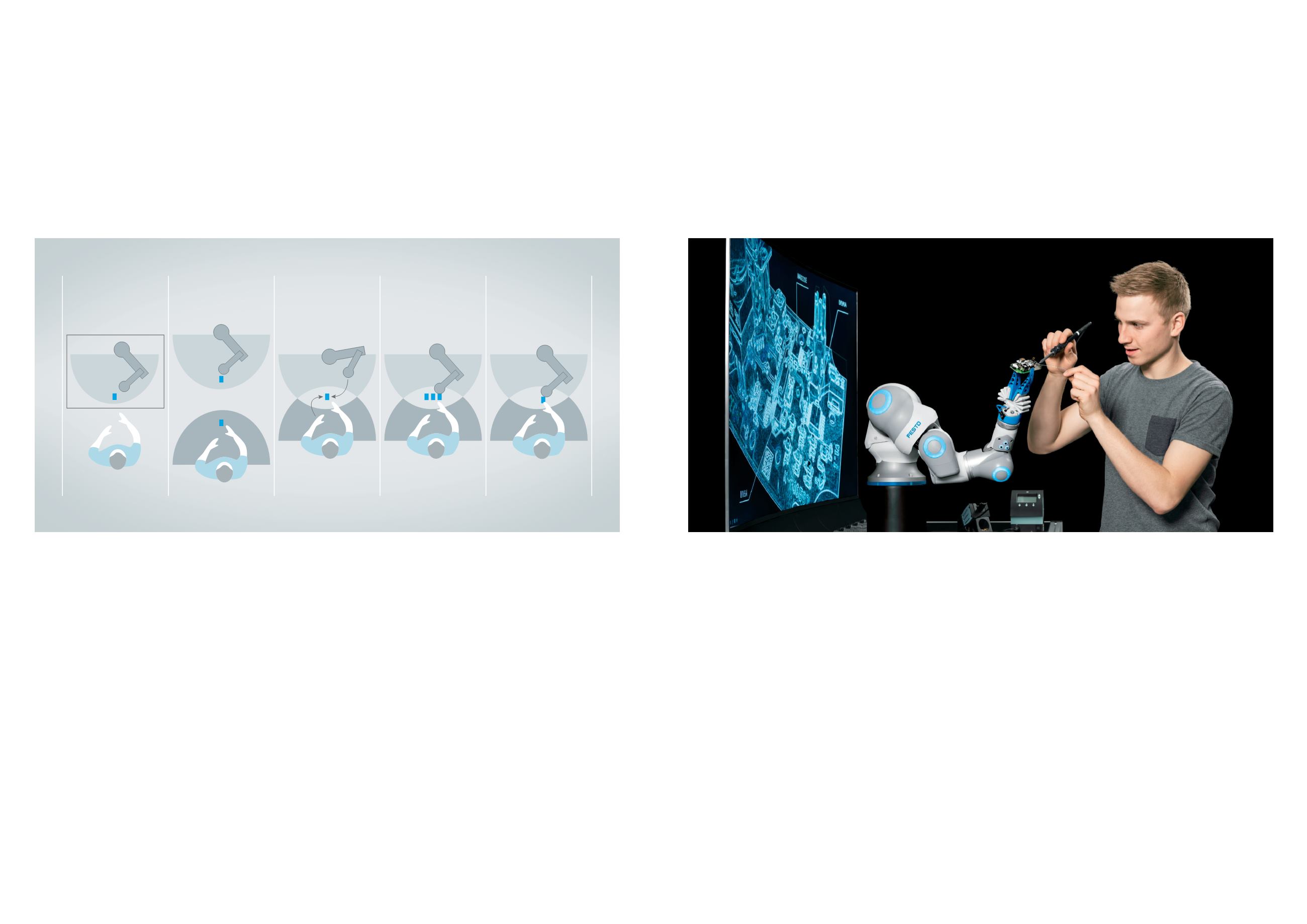
Cell
Coexistence
Synchronised
Cooperation
Collaboration
BionicCobot
Sensitive helper for human-robot collaboration
Whether it is shorter lead times, faster product life cycles or high
flexibility with regard to quantities and variety, the requirements of
the production of the future are manifold and are changing faster
than ever before. This industrial change requires a new way for
humans, machines and data to interact.
Besides the digital networking of entire facilities, above all robot-
based automation solutions, which work hand in hand with peo-
ple, play a critical role in this development. In the production of
tomorrow, direct interaction between man and machine will be part
of the daily routine.
Collaborative working spaces of the future
The strict separation between the manual work of the factory wor-
ker and the automated actions of the robot is being increasingly
set aside. Their work ranges are overlapping and merging into a
collaborative working space. In this way, human and machine will
be able to work together on the same workpiece or component
simultaneously in future – without having to be shielded from each
other for safety reasons.
Being at the forefront of industrial automation, it is Festo’s core
business to help shape the production and working worlds of the
future. A key element for coming up with ideas is the Bionic Lear-
ning Network. In an alliance with external partners, Festo looks for
natural phenomena and operating principles that can be transfer-
red to technology.
Paradigm shift in robotics
At the focus of the current research work are lightweight bionic
robots, which due to their natural movement patterns and the
pneumatics employed are almost predestined for collaborative
working spaces and in future will be able to represent a cost-
effective alternative to classic robot concepts.
The strengths of pneumatic drives have always lain in their simple
handling and robustness, the low costs of acquisition and their
high power density – in other words comparatively large forces
in a small space and with a low weight. Holding processes get by
without further compressed air consumption and are therefore
extremely energy efficient.
For direct contact between human and machine, pneumatics offer
another critical advantage, however: their system’s inherent flexibi-
lity. If an actuator is filled with compressed air, the motion genera-
ted can be exactly set in terms of speed, force and rigidity. In the
event of a collision, the system eases off, thus posing no risk to
the worker.
To be able to adjust the whole system to any settings in its dyna-
mics, the valve technology used must be able to control the air
flows and pressures with extreme precision and at the same time
ensure the complex interconnections of many channels.
Digitisation of pneumatics
What could only be implemented with a great deal of effort until
now is made easily possible by a world first from Festo: the Festo
Motion Terminal is the first pneumatic automation platform, which,
using its software control system, combines the functionalities of
over 50 components using apps. Digitisation is opening up com-
pletely new areas of application for pneumatics, which until now
have been the reserve of electrical automation.
Festo Motion Terminal for controlling complex kinematics
The Festo Motion Terminal combines high-precision mechanics,
sensor technology as well as control and measuring technology
in the tightest space. With the internal control algorithms of the
Motion Apps and the installed piezo valves, flow rates and pressu-
res can be exactly dosed and also varied to any setting in several
channels simultaneously. That enables both powerful and fast,
as well as soft and sensitive motion sequences.
Flexible robot arm with seven degrees of freedom
With the BionicCobot, Festo has now developed a pneumatic light-
weight robot with seven degrees of freedom for the first time,
which due to this flexibility can work together with humans directly
and safely.
In terms of its kinematics, the robot is based on the human arm.
Like its biological role model, it solves many of its tasks with the
help of sensitive movements. Due to its unique drive concept,
which works according to the agonist-antagonist principle, the
motion dynamics and rigidity can be variably adjusted.
01:
Collaborative working space:
Simul-
taneous, common processing of a work-
piece by human and robot
02:
Conceivable future scenario:
The
BionicCobot as a supporting assistance
system in assembly
01
02
© Fraunhofer IAO, study of lightweight robots in manual assembly
2
Festo AG & Co. KG
3
BionicCobot: Sensitive helper for human-robot collaboration