
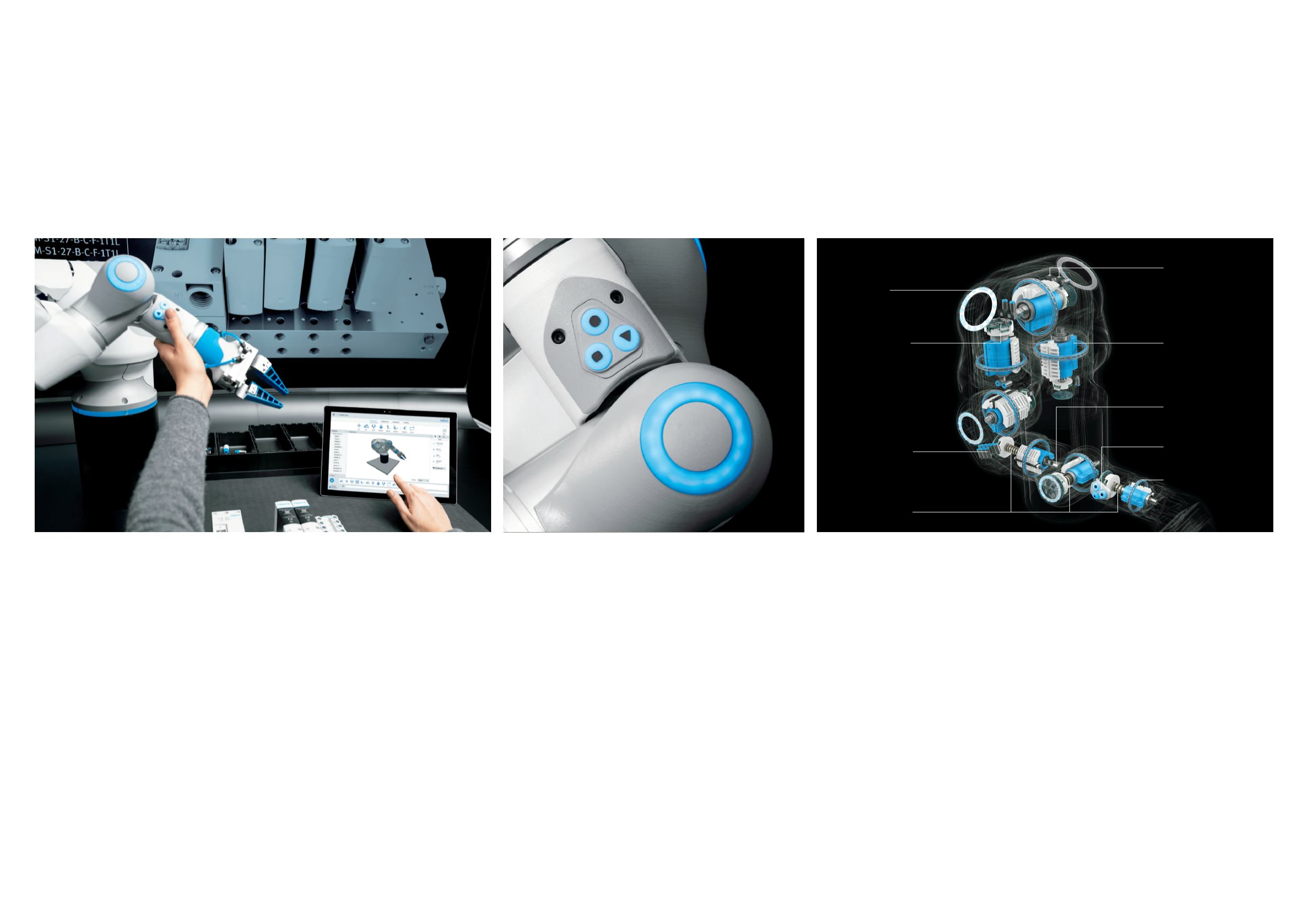
Mode of operation and potential uses
For a safe and more ergonomic future working world
The BionicCobot is operated intuitively by means of a graphic user
interface developed in house. The user can use a tablet to quite
easily teach the actions to be performed and set their parameters.
In this respect, the defined work steps can be arranged in a time-
line in any order using drag and drop. In doing so, the complete
motion sequence is virtually depicted and simulated at the same
time.
Software architecture with three levels
The interface between the tablet and the Festo Motion Terminal
is the ROS (Robot Operating System) open source platform, on
which the kinematics’ path planning is calculated. In addition,
the ROS interprets the incoming code from the tablet and forwards
the resulting axis coordinates to the Motion Terminal.
Based on the coordinates received, the Motion Terminal can use
its internal algorithms to regulate the respective pressure in the air
chambers and hence determine the position of the individual axes.
The incoming sensor data from the seven joints is also channelled
into the actions in real time.
Construction and drive concept based on a natural role model
The construction of the BionicCobot is the same as the human
arm from the shoulder to upper arm, elbow, ulna and radius down
to the wrist and the gripping hand.
Like the blood vessels and nerve fibres in the human body,
the compressed air lines run safely inside the construction and
thus cannot become bent. They supply the pneumatic rotary
vane drives, which are located in the seven joints of the robot arm.
Installed in each joint are also two pressure sensors and an abso-
lute encoder with CAN bus for determining the positional data.
If compressed air is supplied to the air chambers in the drives,
the rotary vanes move in a certain direction, which is transferred
to the integrated bearing shafts. From the elbow downwards, all
the lines down to the gripper are laid directly through the shafts.
Special packing cartridges enable this rotary through-feed of up to
six channels, of which two air lines ultimately supply the gripper.
Depending on the task, different gripping systems can be connec-
ted to the BionicCobot.
The technical implementation of the agonist-antagonist principle
allows the force potential and hence also the rigidity level of the
robot arm to be exactly determined. In so-called balancer mode,
the BionicCobot is controlled in such a way that it balances gravi-
tational force and payload and can calmly hold a desired position
immediately. The holding process is done almost without energy
and is ideal for assembly activities.
Safe collaboration and high user acceptance
Apart from the tablet interface, the user also has a manual con-
trol panel on the gripping joint at their disposal. The robot can
communicate with the user via signals from the blue LED lighting
on the joints – for instance to indicate a waiting mode or to send
warnings.
If, despite this, there is a collision, the robot arm automatically
gives way and poses no danger for humans. By using pneumatic
semi-rotary drives, the system cannot overheat. In addition, the na-
tural movements of the bionic robot arm create a sense of familiarity
for the user, which increases acceptance for working together.
Many possible applications to relieve humans
In future, the BionicCobot could relieve humans in many places
where monotonous and mindless or even dangerous and un-
healthy motion sequences are involved. It improves the ergono-
mics at the workplace and increases productivity. Particularly in
production, manual work, service or maintenance, the pneumatic
lightweight robot could be used to partly automate work steps
simply and economically.
Conceivable future scenarios
In future the system can be flexibly extended and enhanced if
required: for instance by adding speech control, image processing,
infrared tracking or artificial intelligence. The specially developed
software technology, such as the user interface, can also be trans-
ferred to other robot kinematics.
As the BionicCobot can also work in dirty or unhealthy environ-
ments, it is also predestined for use in telemanipulation: with the
aid of VR goggles, a person could be made able to control the
robot arm as intuitively as his own arm.
01:
Intuitive operability:
The robot arm
can easily be taught using the tablet
interface
02:
Safe handling:
The manual control
panel and one of the LED rings for com-
munication with the user
03:
Sophisticated interaction:
The new
drive concept of the seven-axis robot
arm
Ring-shaped
LED lighting
Pressure sensor pair
Air distribution
panel with QS
screw connections
Bearing shaft with
energy feed-through
Packing cartridges
Adjustable bearing
Manual control panel
Absolute encoder
with CAN bus
Pneumatic
rotary vane
01
02
03
6
Festo AG & Co. KG
7
BionicCobot: Sensitive helper for human-robot collaboration