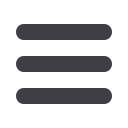
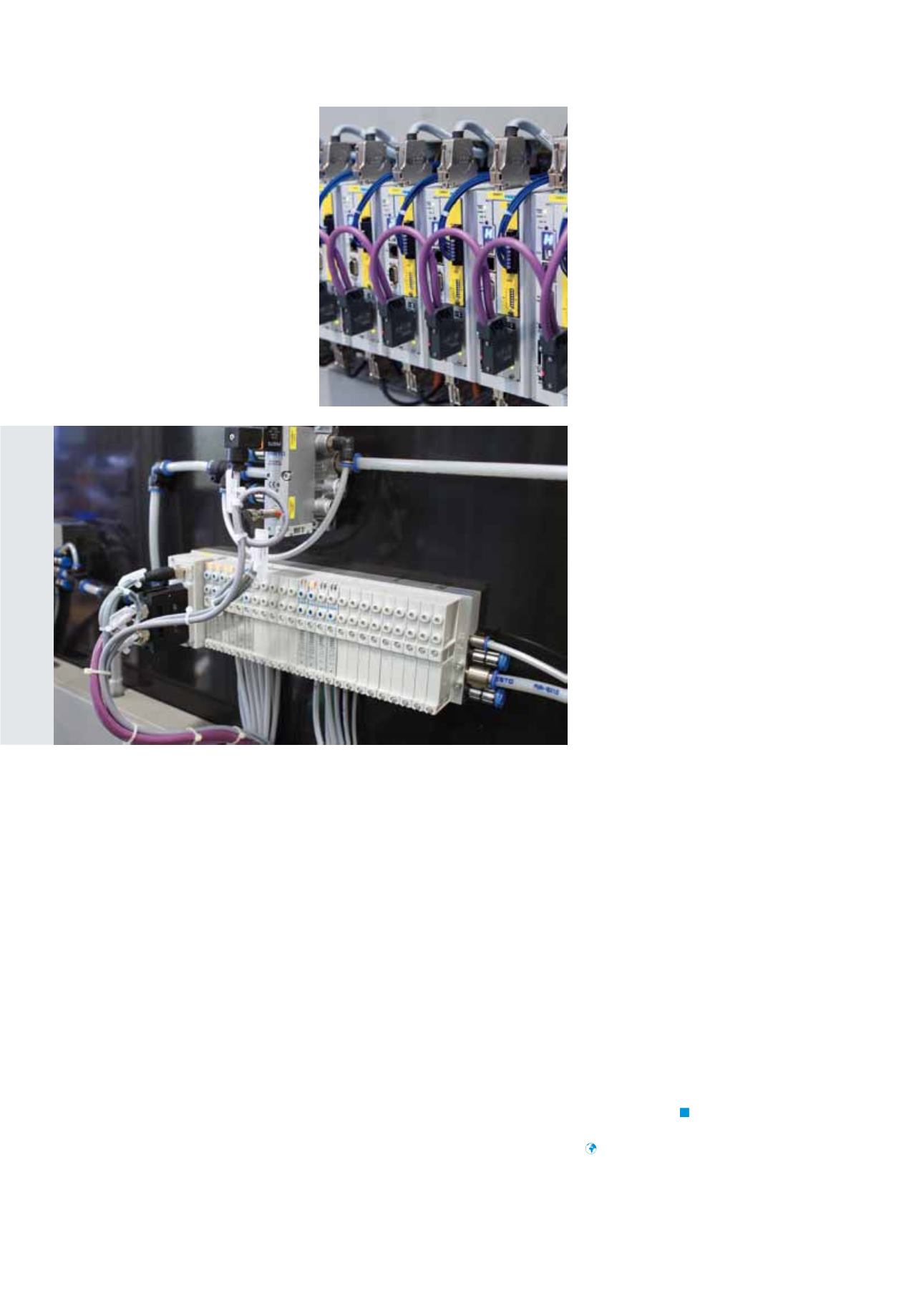
Hier sind zwei Zahnriemenachsen Typ
EGC-80 mit Führungsschlitten, synchroni-
siert über eine Verbindungswelle, mit ei-
nem platzsparenden Winkelgetriebe im
Einsatz (x-Achse). Außerdem eine Schwer-
lastachse mit robuster Doppelführung Typ
EGC-HD-160-BS (y-Achse), sowie ein Flan-
schgetriebe Typ PLFN. Alle Achsen sind
ausgerüstet mit Servo-Antriebspaketen
mit Multiturn-Encodern.
Projektleiter Legat ist begeistert von den
einbaufertigen Handlinglösungen: „Wir ha-
ben nur die Kenndaten bekannt geben, die
Lasten und dieWege oder Bahnen definiert,
die es zu verfahren gilt, und brauchten uns
über diesen Teil der Anlage keinerlei Gedan-
ken mehr machen. Eine große Arbeitser-
leichterung, ebenso wie die Verwendung
der CAD-Daten der Handlings, die uns von
Festo für die Konstruktion der Gesamtanla-
ge zur Verfügung gestellt wurden.“
Das Vernieten
Die auf dem Handling montierten Nietkopf-
werkzeuge werden das letzte Stück von
VTUG angesteuerten ADN-Zylindern zuge-
stellt. Die Kontrolle der Stiftlänge an den Re-
flektoren vor demVernieten sowie der kor-
rekten Endposition erfolgt mittels auf den
Zylindern befindlichen SMAT-Positionstrans-
mittern. Passt die Länge des Stiftes, wird
sein vorstehendes Ende thermisch von den
Nietkopfwerkzeugen zu Nietköpfen umge-
formt. So entstehen dauerhafte Verbindun-
gen, die die sensiblen Einzelteile ein Fahr-
zeugleben lang an ihrer Position halten.
Nun wird das fertige Bauteil, bestehend aus
Kühlkörper, Platine und den vernieteten Re-
flektoren, vom Bediener entnommen und in
den Scheinwerfer eingebaut.
Controller vom Typ CMMP
mit
integriertem Sicherheitsmodul
steuern die Handlings in den
Bereichen Wärmeleitpasten
auftrag und Warmvernietung.
Eine VTUG-Ventilinsel
versorgt die Pneumatik auf
der Lichteinstellstation.
Auszugsprüfung
Um den festen Sitz der Komponenten zu
überprüfen, kommt der Scheinwerfer in
die Auszugsprüfstation, wo mit pneuma-
tischen Dreh-Hubantrieben Haken unter
das Modul gefahren werden, um an-
schließend durch Zug seinen festen Sitz
zu überprüft. Anschließend geht es zur
Lichteinstellstation. Der Bediener legt
den Scheinwerfer auf einen Drehteller.
Der Scheinwerfer wird gespannt und der
Teller in Arbeitsposition geschwenkt.
Dann können der Scheinwerfer kontak-
tiert und die unterschiedlichsten Lichtbil-
der sowie das Blinkmodul mittels Kame-
ras überprüft werden. Außerdem wird
hier die korrekte Position des Leuchtmo-
duls kontrolliert und - wie in einer Auto-
werkstatt - auf das ideale Niveau einge-
stellt.
Finale Schritte
Danach werden die Designblenden mon-
tiert, die die gesamte Technik abdecken,
und in einer Klebezelle die äußere, durch-
sichtige Linse (Front des Scheinwerfers)
mittels silikonfreiem Warmmelt-Kleber
aufgeklebt. Ein zeitkritischer Prozess, da
die Teile mit dem Kleber nur in einem be-
stimmten Zeitfenster optimal verbunden
werden können. Nach dem Vorerwärmen
zur Reduktion der Oberflächenspannung
und dem Aufbringen des Klebers ver-
presst ein Roboter die Linse mit dem
Scheinwerfer-Gehäuse. Anschließend er-
folgt eine Dichtheitsprüfung des Schein-
werfers. Besteht er diese, ist ein weiterer
innovativer Lichtbringer fit für seine Reise
durch die Welt.
www.vescon.at