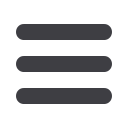
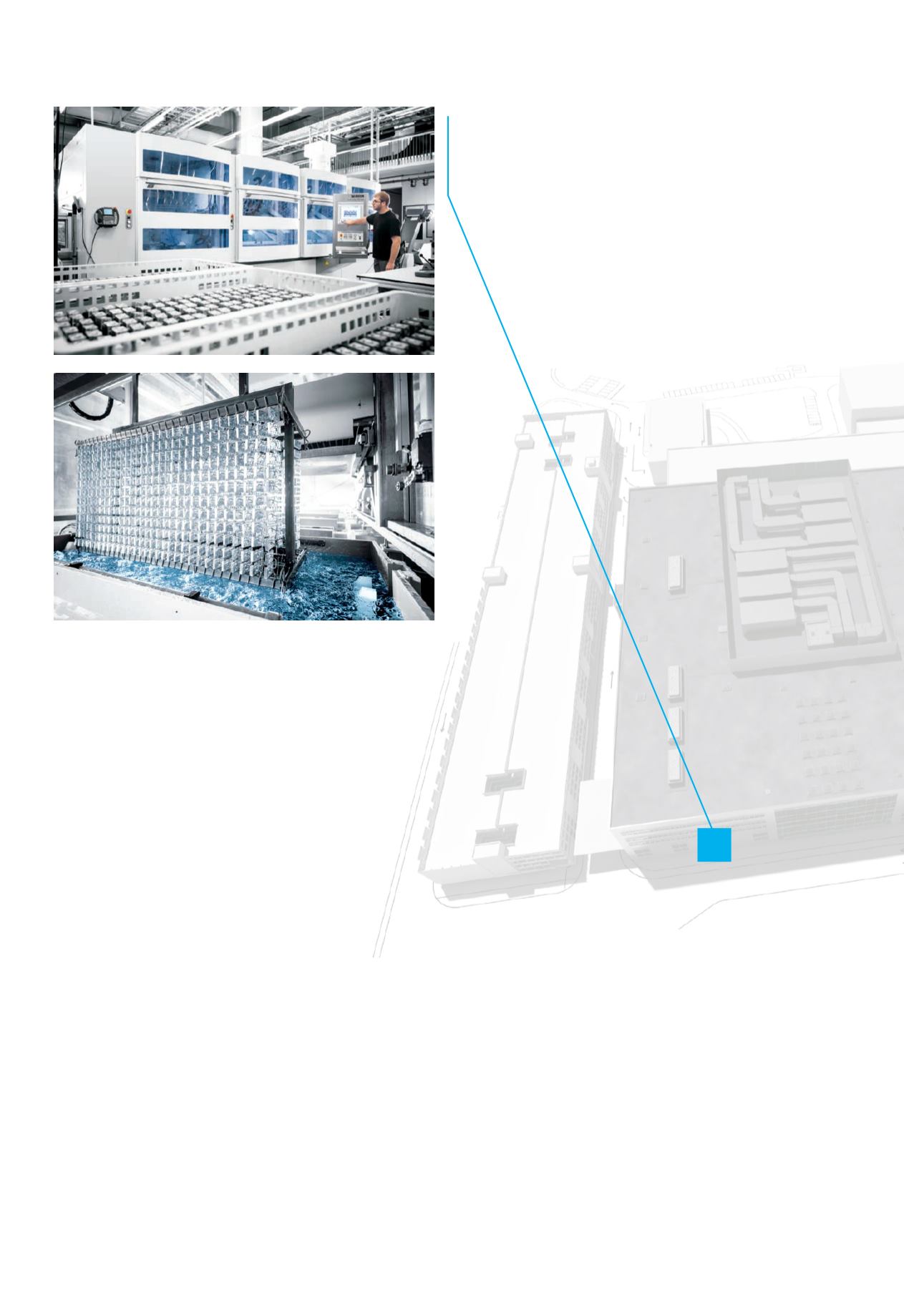
The components are immersed
in electroplating tanks
to give them the necessary surface properties.
place in a space measuring just 120
metres inside the Technology Plant. High-
quality products, valves and valve
terminals, electronic components and
customer solutions are thus produced
under one roof in a very short space of
time.
In perfect shape
The Technology Plant is divided into
four
areas: (1)
machining,
(2)
assembly,
(3)
electronics manufacturing and
(4)
customer solutions.
Metal-cutting machines weighing several
tons stand in an area covering 14,000
square metres on the ground floor of the
Technology Plant. Turning, milling, drilling
and grinding – in the machining
department, precision components made
of metal are manufactured for further
processing in the assembly process. The
production lines work around the clock to
produce the basic elements for Festo
products, such as valve housings and
individual components for linear units.
They produce millions of valve sealing
T
he new Festo Scharnhausen
Technology Plant symbolises
cutting-edge automation: 66,000
square metres, 1,200 employees,
a sophisticated, highly efficient value
chain, open communication with the
Learning Factory and creative think tanks.
Networked systems enable the first
Industry 4.0 technology solutions to be
created. Every day employees interact
directly and safely with a flexible robot.
Information and materials flow quickly,
flexibly and reliably in seamless value
streams.
Short routes
In the lean Technology Plant, the individual
manufacturing processes are linked to
each other by the shortest of routes. They
are arranged so that, as far as possible,
there is no need for interim buffering
across warehouse stocks. For example,
while some processes used to be
distributed across several plants over a
distance of 32 kilometres, they now take
Machining department with electroplating
In an area covering 14,000 square metres,
the
highly automated production lines work around
the clock to produce the basic parts for Festo
components.
1