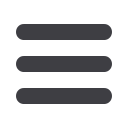
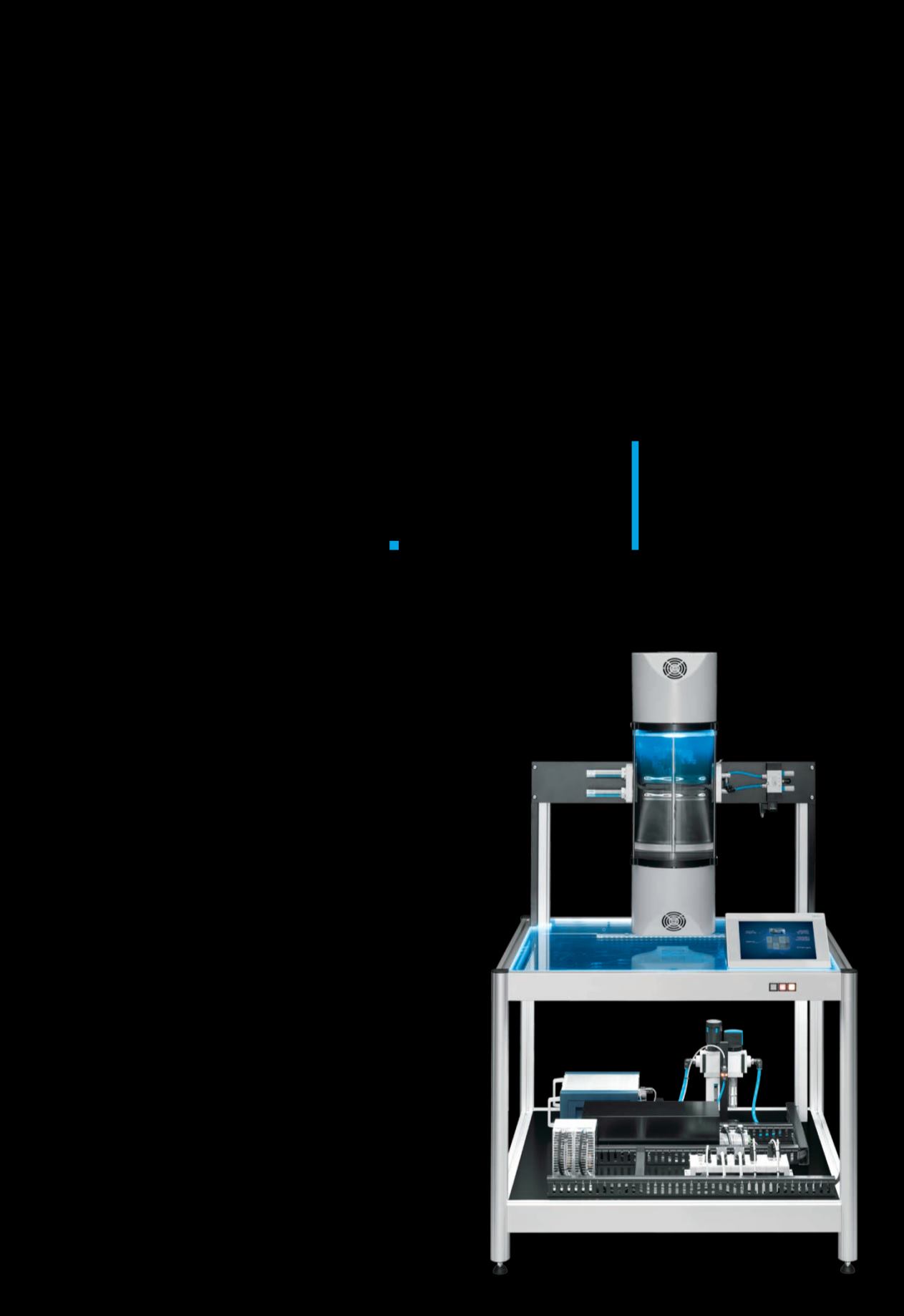
Throughout this process, the plates hover
over a flat basin of water. The carrier
system and the automation mechanism
are thus entirely separated from each
other. This protects the components
against dirt and facilitates cleaning – ideal
for applications in the packaging industry,
laboratory automation, medical
technology, or the food and
pharmaceutical industries.
SupraGripper works in separate spaces
With SupraGripper, two grippers, each
with three gripper fingers, levitate freely
above two semicircular plates. This
technology enables objects to be grasped
and transported within enclosed spaces –
a practical solution for cleanrooms or for
working in liquids, gases or in a vacuum.
The levitating effect is generated by three
cryostats, which are installed beneath the
plates and can be driven up or down. The
grippers thus either levitate above the
plates or are placed on them. In addition,
the two plates can be rotated and precisely
positioned by two rotary drives, so that
the two grippers can be transported from
one cryostat to the next.
To grasp an object, electric coils fitted on
the cryostats emit an impulse, which either
severs the stored connection to the
magnetic gripper elements or restores it
as required. This impulse causes the
individual finger elements to fold up or
down, making the grippers open or close.
SupraTube rotates within a tube
The SupraTube exhibit shows how a
controlled movement can be executed
within a tube without direct intervention
from the outside. A round cryostat with
superconductors is attached to the
outside of each end of a liquid-filled glass
tube. Inside the vertical tube is a magnetic
puck that is virtually tethered to the two
cryostats with a levitation gap of around
five millimetres and is initially suspended
beneath the upper cryostat. A ring magnet,
which surrounds the cryostats, is set to
rotate by a stepper motor, and transfers
the motion to the suspended magnet. The
magnet is repelled from the cryostat by an
electrical impulse and drifts downwards in
a spiral motion. At the lower end, it is
captured once more and centred by the
superconductor in the other cryostat.
In a slightly modified SupraTube
configuration, drive units with
superconductor magnetic couplings can
be fitted along the longitudinal axis of the
tube in order to draw a cleaning unit
through it, entirely free of contact.
Alternatively, the contents of a closed
container – such as hazardous substances
or explosive gases – can be set in
rotation.
Research for the production of the future
After several years of intensive research
and three years of experience in this field
at trade fairs, Festo is now meeting with
partners and customers to discuss and
explore their specific ideas for application.
“We have now created 12 different
concepts that have really inspired our
customers and given them lots of ideas
for new applications,” says Georg Berner.
He and his team are currently working on
getting the first pilot projects off the
ground.
SupraTube
executes a movement inside a tube
without direct intervention from the outside.
More information on
superconductor technology
and the new projects
can be found at
www.festo.com/supramotionIssue 30
trends in automation
Compass
16
–
17