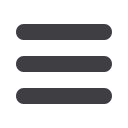
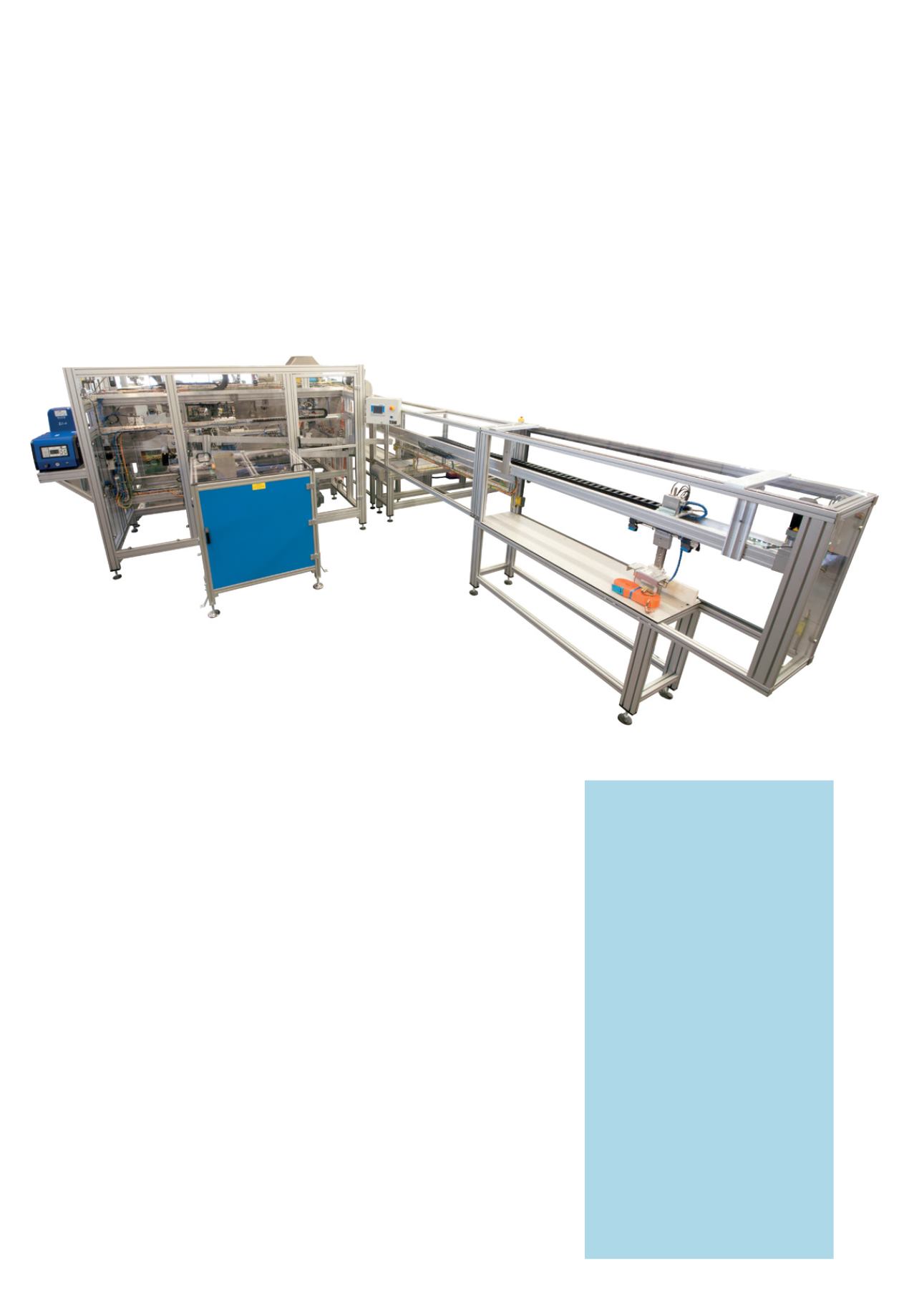
« De uitdaging was om de gevraagde
cyclustijden te halen in combinatie met
de strenge kwaliteitseisen voor veilig-
heidscomponenten. »
Ballieu Klaas, Projectingenieur TMC Machines
E
en producent van spanbanden
zocht een geautomatiseerde op-
lossing voor zijn productie. TMC
machines ontwierp hiervoor een
volledig geautomatiseerde productielijn.
Deze bestaat uit drie delen: deel 1 maakt
volautomatisch rollen met haak, in het
tweede deel werkt een operator de korte
delen met ratels af en door het derde deel
worden ze samengevoegd in een intelli-
gent buffer.
St(r)ikt machinaal
In het eerste deel worden band, haken,
labels en garen uit bulk gebruikt. Dikte-
meting en metaaldetectie worden ingezet
om kwaliteitstekortkomingen op te sporen.
Haken worden met behulp van een pick
and place naar de vouwpositie gebracht.
In deze positie wordt het band rond de
haak gevouwen door middel van servop-
neumatische componenten. Aangezien de
grondstof een geweven product is, is deze
niet altijd maatvast of recht. Tijdens deze
manipulatie is het van zeer groot belang
dat de machine de band steeds blijft vast-
houden. Het is een spelletje van grijpen
en overnemen zodat de band in alle stap-
pen onder controle blijft. De labels met
gewenste gegevens worden afgesneden
en met een vacuümgenerator met feed-
backsignaal op de juiste plaats inge-
voegd. Dit geheel wordt zowel naar de
CNC gestuurde naaimachine getranspor-
Bandwerk
De uitdaging: gevraagde cyclustijd in combinatie met de strenge kwaliteitseisen
TMC Machines uit Ieper is gespecialiseerd in machines
voor narrow fabric textiles.
Al 15 jaar lang leveren ze oplossingen aan de textielindustrie: van heavy duty cnc
naaimachines, snij- en wikkelmachines tot volledig geautomatiseerde productielijnen.
Om efficiënter en sneller te werken is een bijkomende firma voor 3D-printing opgericht.
De machine maakt veiligheidsproducten
die onderworpen zijn aan strenge
eisen. Fouten vermijden of uitfilteren is essentieel waardoor diagnose en
feedback prominent aanwezig zijn in de architectuur van de machine.
Oplossingen in 3D
Om plooi-, frees- en draaiwerk tot
een minimum te herleiden werd
een 3D-printer aangeschaft. Veel
componenten kunnen worden ge-
print wat heel wat winst met zich
meebrengt in volgende productie-
stappen. Zo worden veel bevesti-
gingsblokjes geprint voor bijvoor-
beeld sensoren, maar ook
complexere componenten kunnen
ontworpen worden. Zo is bijvoor-
beeld de slede waarin de ratels en
haken vastgemaakt worden op
maat geprint, alsook werd een
venturi ontworpen en geprint met
exacte afmeting en oriëntatie die
nodig waren om een naaigaren te
kunnen evacueren. Ruimtelijk per-
fect geïntegreerd in het proces, en
van alle mogelijke adapters en
connecties voorzien. Om de inves-
tering te rentabiliseren wordt ook
voor derden geprint.