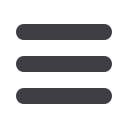
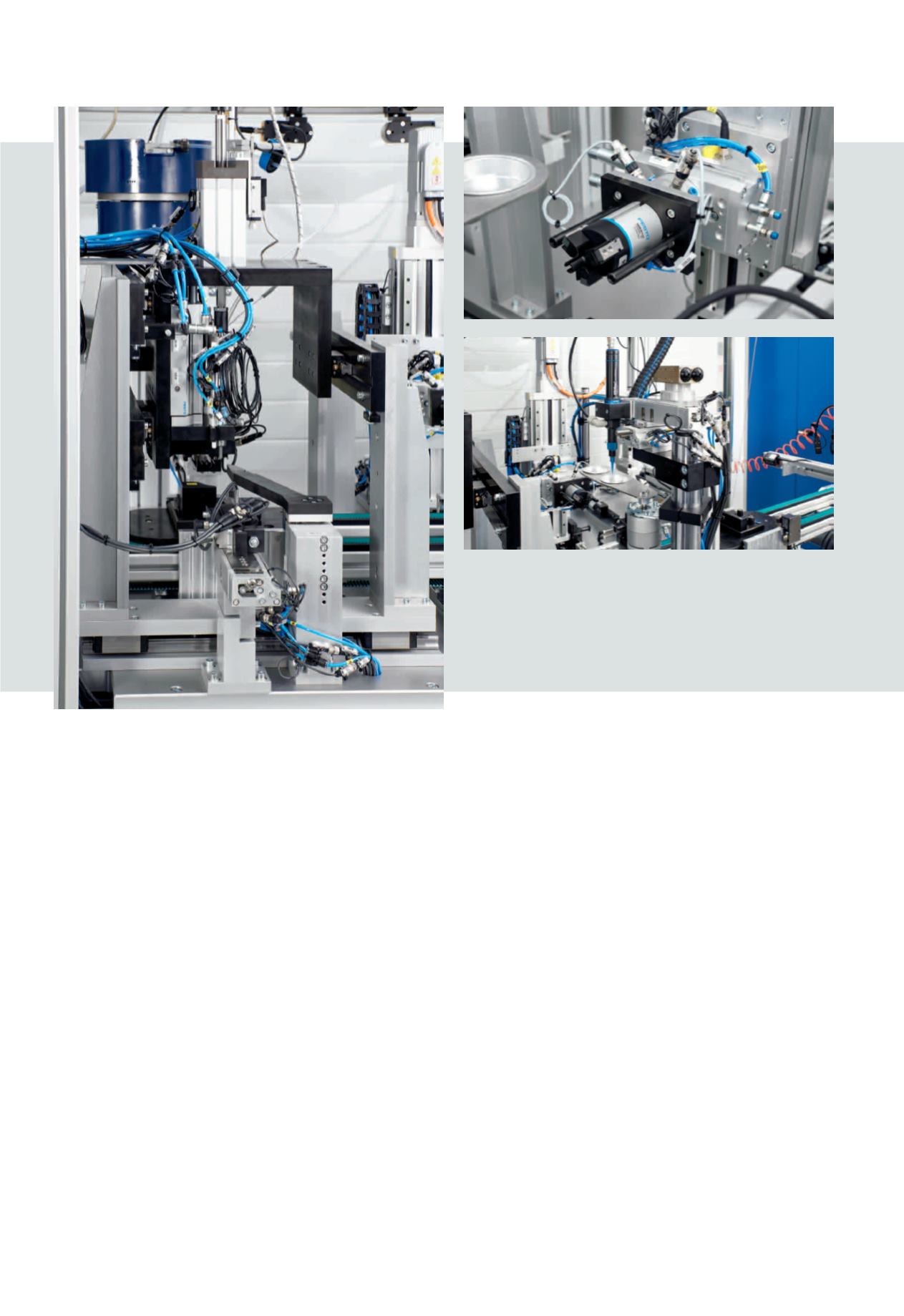
(A) Die erste der drei vollautomatisierten Arbeitsstationen
dreht
den Werkstückträger per DRSL Zylinder um 180 Grad und fixiert ihn
mit einem per DGSL Mini-Schlitten gesteuerten Niederhalter.
(B) Kolbenschwenkantrieb DRRD
mit Dreipunktgreifer DHDS für das
Aufnehmen des Werkstücks zur transportbandschonenden Bearbeitung.
(C) Ein Schwenkantrieb DRVS
fährt zwei Abtropfschalen unter die
Dosierdüse und schützt die Anlage so vor Verschmutzung.
Lesekopfs ausgewertet werden können.
Danach fixiert ein Niederhalter, als Kom
paktzylinder ADN ausgeführt, das Kunst
stoffgehäuse des Luftmengenreglers. Im
Anschluss legt ein Werker die Welle für
die Drosselklappe ein, die im weiteren
Prozessverlauf hinzugefügt wird. Eine
elektrische Linearachse EGC verfährt den
Werkstückträger in die für die typbedingt
unterschiedliche Wellenlänge passende
Vorposition. Die pneumatische Linear
achse DGC bewegt einen Pilotierdorn in
die Endlage. Per Druckumschaltung wird
dann die Welle mit dem Pilotierdorn in
das Bauteil eingeschoben. Nach dem Ver
fügen legt der Werker die Drosselklappe
händisch in die Passungen der Welle ein.
Punktgenau fixiert
An der ersten von drei vollautomatisierten
Arbeitsstationen wird zunächst der Werk
stückträger per DRSL Zylinder um 180 Grad
gedreht und mit einem über DGSL Mini-
Schlitten gesteuerten Niederhalter fixiert.
Danach erfolgt die Anwesenheitsprüfung
von Nadelbuchse und Nadellager, die
beidseitig die Drosselklappenwelle um
schließen. Gleichzeitig wird diese auf ihre
richtige Position zur anschließenden Ver
pressung eines Fixierstifts ausgerichtet.
Damit der Stift an werkstückspezifisch
unterschiedlichen Punkten eingeschossen
werden kann, bewegt ein Rundzylinder
DSNU den kompletten Halteapparat des
Werkstückträgers auf Position.
Die zweite automatisierte Arbeitsstation
löst zunächst das Werkstück per Kolben
schwenkantrieb DRRD mit Dreipunktgrei
fer DHDS vom Band, sodass die Bearbei
tungskräfte sich nicht negativ auf das
Transportband auswirken. Nach dem Ver
fahren in die Bearbeitungsposition werden
die Enden der Fixierstifte mit einem Kunst
harz beträufelt. Um die Stiftenden auf
beiden Seiten der Luftmengenregler zu
erreichen, schwenkt die Arbeitsstation das
Werkstück um 180 Grad und anschließend
wieder zurück in die Ausgangsstellung.
Währenddessen verfährt ein Schwenkan
trieb DRVS zwei Abtropfschalen unter die
Dosierdüse, um die Anlage vor Verschmut
zung zu schützen.
Intelligent Zeit gewonnen
In der dritten Arbeitsstation zum Aushärten
des Klebers per UV-Licht lassen sich gleich
zeitig zwei Werkstücke bearbeiten. Nach
dem das eine gegriffen und um 180 Grad
zur UV-Station transportiert wurde, kann
schon das nächste aufgenommen werden,
das im Anschluss zum Aushärten trans
portiert wird. Bei einer Anlagentaktzeit
von nur 13 Sekunden lässt sich die Aus
härtezeit damit verdoppeln. Für eine opti
male Positionierung der oberen von zwei
UV-Leuchten sorgt der Zwischenanschlag
des Mini-Schlittens DGSL. Der DGSL
Schlitten wurde aus Platzgründen mit
(A)
(B)
(C)