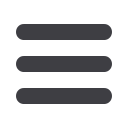
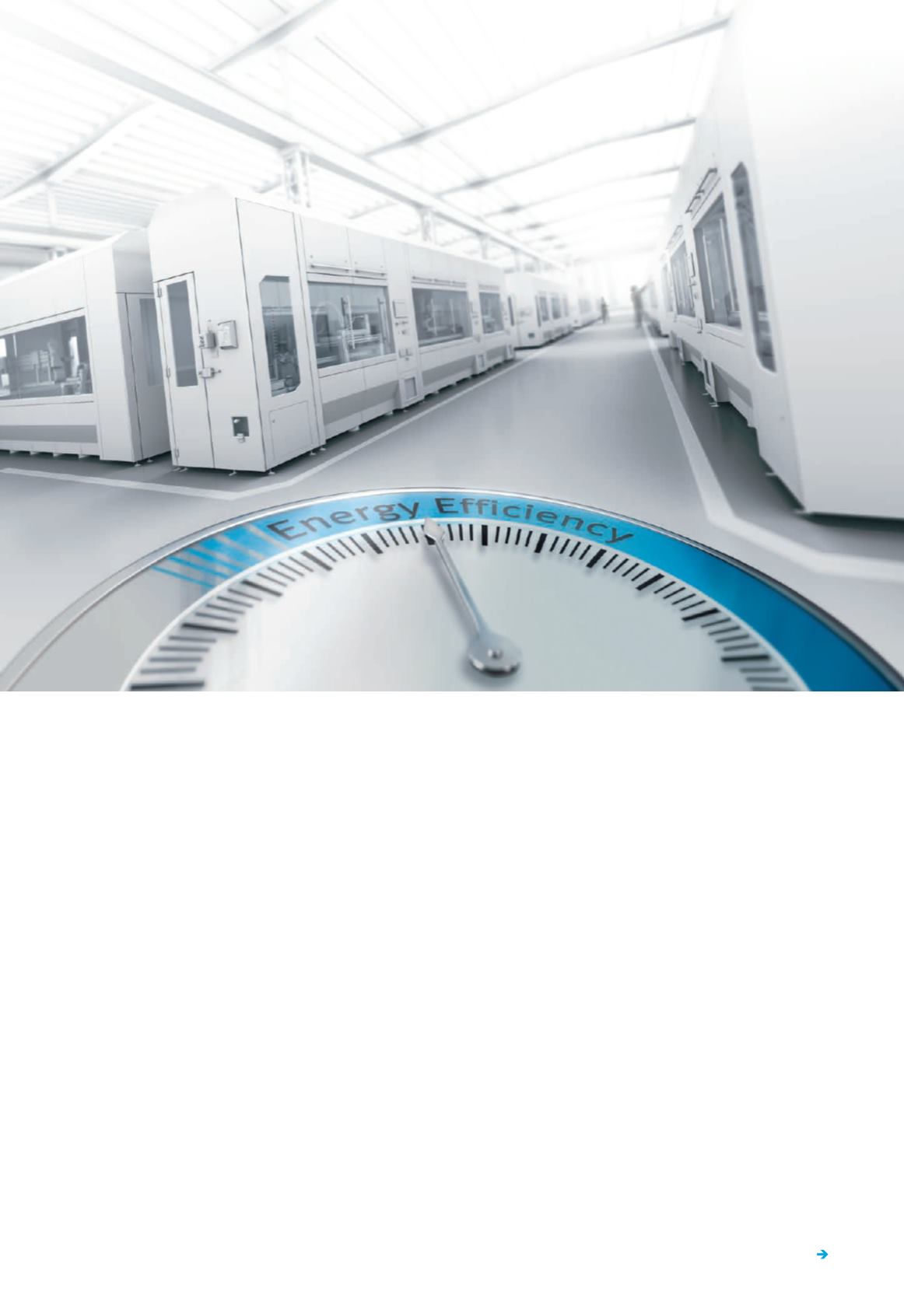
Issue 30
trends in automation
Impulse
24
–
25
Many companies struggle
to reach their energy saving targets,
even a 5-10% KPI to reduce energy spend is a big ask.
Bringing energy
efficiency into view
Gary Fuller, Training & Consulting Programme Manager, Festo
A
s a manufacturer ourselves,
we are focused on eliminating
waste, improving productivity
and reducing our environmental
impact. We are naturally very high users
of our own automation equipment and
strive to do so in the most efficient way
possible. To do this we have implemented
a diverse and wide ranging strategy to
reduce energy consumption and have
gained a lot of experience internally. We
also work with many other leading
manufacturers and there’s one thing that
we’ve found – saving costs on
compressed air is not simple. Here are
some of the reasons why.
Compressed air costs aren’t understood
Many users don’t know or appreciate the
cost of energy, compressed air in
particular has frequently been seen as a
fixed cost asset, “the compressor is there
anyway” and therefore a “free” resource.
However, with the cost of electricity nearly
doubling over the last 12 years and
electricity consumption being 60-70% of
the total cost of compressed air it can be
an expensive resource and certainly not
one to be squandered. The low hanging
fruit for reducing compressed usage is
always considered to be leaks – where
we’re literally blowing money away.
There are some great headline grabbing
figures which are frequently quoted often
resulting in excitement about fixing