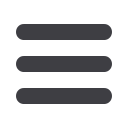
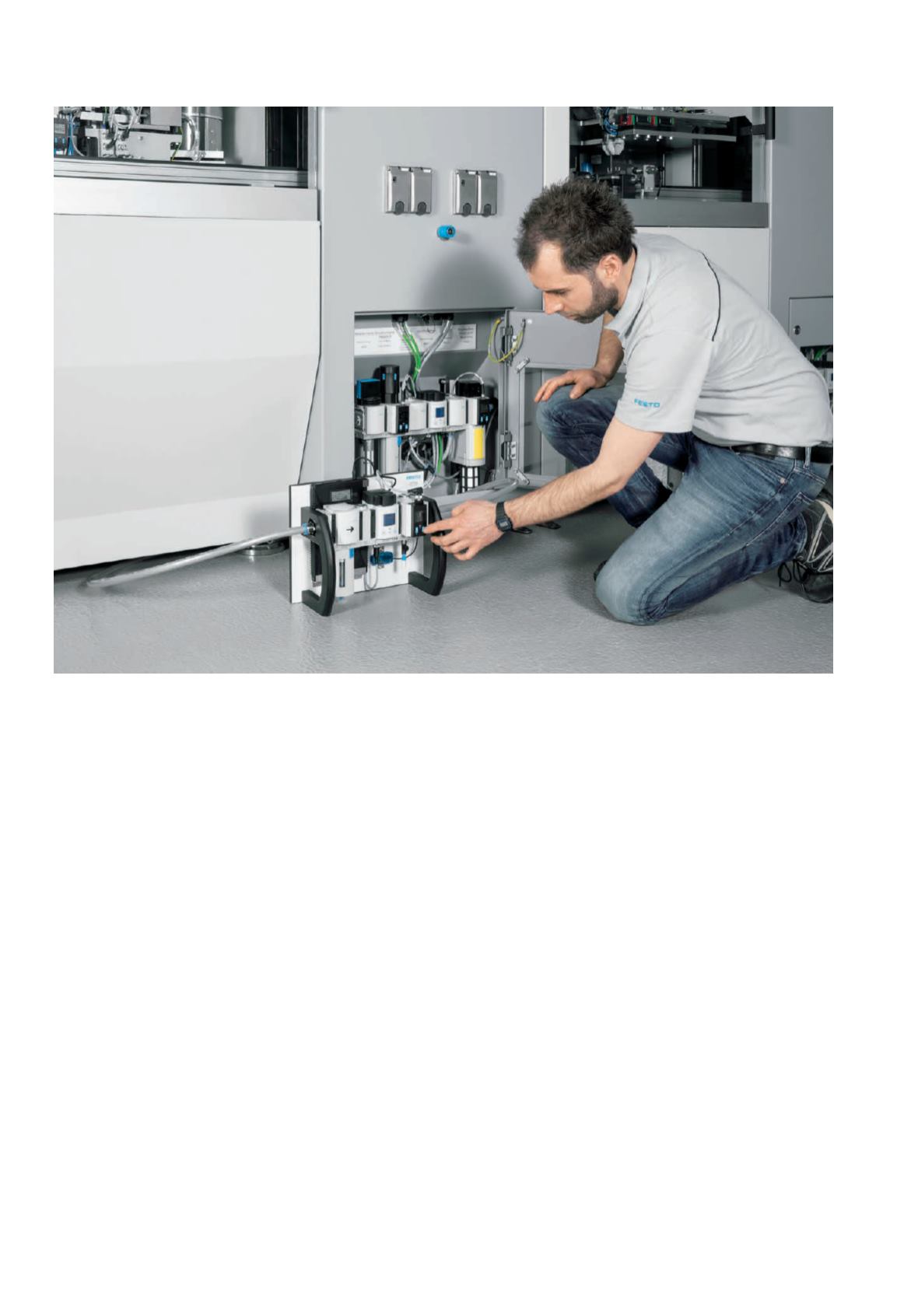
leaks in compressed air systems. Typically
purely electric drive manufacturers will
cite older European reports showing that
42% of the cost of compressed air is lost
in leakages. That’s when leak
identification reports are commonly
commissioned.
However, alone, this rarely produces the
anticipated results, in fact frequently the
identified leaks aren’t fixed at all. It’s not
unusual when surveying pneumatic
systems that we’ll see leakage tags still
there years after being marked.
Consciously or unconsciously
incompetent?
Not understanding the value of
compressed air means that it is frequently
forgotten and overlooked, this
‘unconscious incompetence’ means
engineers, operators, maintenance staff
or the many other people who walk past
leaks, poorly designed or maintained
machinery day after day, don’t see it as
part of their job to report or fix problems.
Energy reduction has to become a shared
and embedded responsibility using tools
such Balanced Score Cards and KPIs.
If the team know that something needs to
be done and they’re being measured on
it, they can take the next step to
becoming ‘consciously incompetent’; a
vital step as they will now seek ways to
improve the situation and start to be part
of the cure rather than the cause.
To make significant changes in the culture
of an organisation the change and focus
has to come from the top. Whether it’s
light bulbs, kettles, machines in stand-by
or an over pressurised regulator it’s only
by everyone taking personal
responsibility that substantive savings
can really be made.
Education is key
The key to this is education;
understanding what can be achieved, to
believe it can be done. It’s about turning
the invisible resource of air into a visible
asset and showing viable ways to reduce
costs. That’s when you’ll make serious
savings and hit your KPIs to reduce the
cost of your energy.
Once this need has been established the
team will need energy consumption
visibility and transparency and the ability
to invest in energy saving measures.
Understanding and monitoring energy
consumption enables the team to
implement actions throughout the
consumption phases. This can start in the
compressor house, investing in the latest
combined heat and power plant,
optimised load sharing compressors and
distribution systems. Capturing and using
the heat energy generated when
compressing air considerably improves
the overall system efficiency. Heat pumps
can even convert this energy into cooling
if that is required or utilised as heating or
an energy source in other processes such
as plating.
Start at the design stage
Retrofitting and upgrading equipment
should be considered but has to be done
against a background of OEM warranties
and the possible need to re-CE mark
equipment if substantial changes are
made. Clearly the best time to optimise
the energy consumption is at the design /
purchase stage. Capital equipment
purchase specifications must lay down
clear expectations in terms of the use of
best energy practise in the selection and
layout of the machine elements.