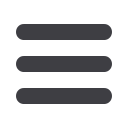
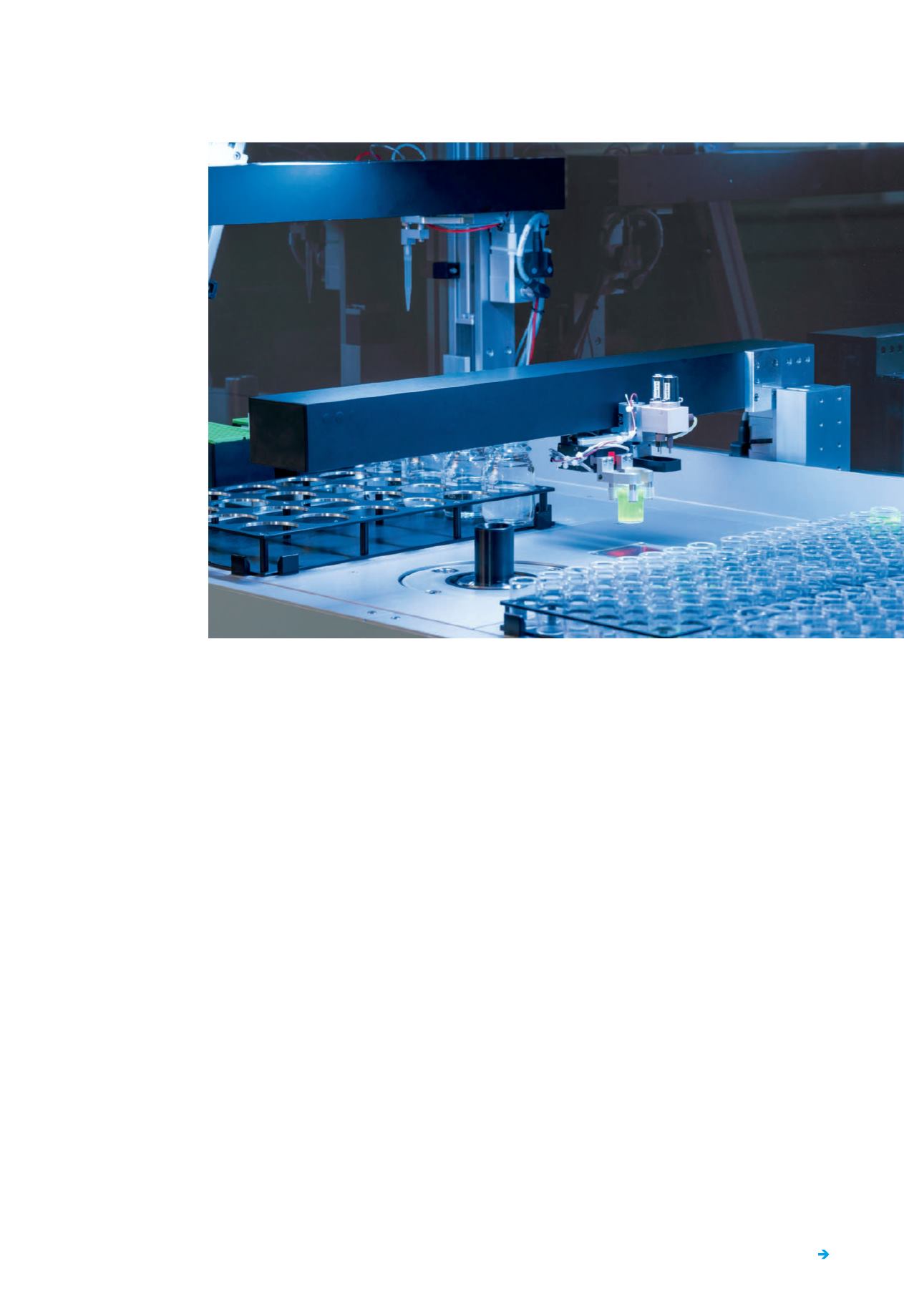
T
he advantages of laboratory
automation are plain to see: it
frees up laboratory technicians
from monotonous, repetitive
tasks, and eliminates the need for them
to handle hazardous substances. It
permits 24-hour operation seven days a
week, and increases the quality,
reproducibility and traceability of
samples. But the most important
advantage for the majority of laboratories
is that automation not only saves time
and money, but also guarantees an error-
free analyses and therefore accurate
results.
Compact bench-top platform
The Modular Sample Processor is a system
for preparing samples, such as for
chromatographic analysis with high-
pressure throughput for samples within a
range from a few up to 100 millilitres – as
required in the petrochemical, food or
fragrance industries. The compact bench-
top platform prepares samples which are
then tested, for example, for their water
content, density, viscosity, suspended
particles or pH value. “We use it for
automating time-consuming manual work
such as pipetting, sampling, dosing and
weighing across a wide range of volumes
and for many different types of samples,”
explains project manager Markus
Schöllauf from the Automation and
Robotics division of Anton Paar. This
ensures the volumes, concentrations and
mixtures are correct. The Modular Sample
Processor can be used as a bench-top
unit for liquid media and solids, or
integrated into complete automation
solutions.
Precise pipetting procedures
Compact handling gantries with electric
axes from Festo – the DGEA axis in the
X-direction and the EGSK axis in the
Y-direction, equipped with motors of the
type EMMS-ST – ensure precise pipetting
procedures. Once a pipetting procedure
has finished, a pneumatic AEN cylinder
from Festo ensures that the used pipette
is ejected into a waste chute.
Another handling system equipped with
the same axes takes the sample holders
from the output trays and places them on
the weighing unit. There, a pipette
provides the sample holders with the
exact amount and volume of the
substance to be tested. The sample
holder is then held by the handling gantry
over a scanner so that the sample can be
allocated using a data matrix code. This
integrated barcode reader enables the
samples to be traced throughout the
entire specimen preparation process. At
the end of this process, the sample is
placed on the output tray.
Tested complete solution
“Festo didn’t just supply us with the axes,
but also a complete system solution
including a CECC CODESYS controller,”
says project manager Schöllauf, reporting
on the cooperation with Festo. He
continues by adding, “Without that, it
would not have been possible for us to
meet the extremely short development
deadline of four months.” This also made
it possible to program the two handling
gantries so they would never collide
despite the fact that they move within the
same working space. This was checked
and tested by Festo before delivery.
Precise pipetting processes:
thanks to compact handling gantries with electric axes from Festo.
Issue 30
trends in automation
Synergies
32
–
33