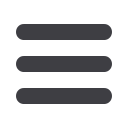
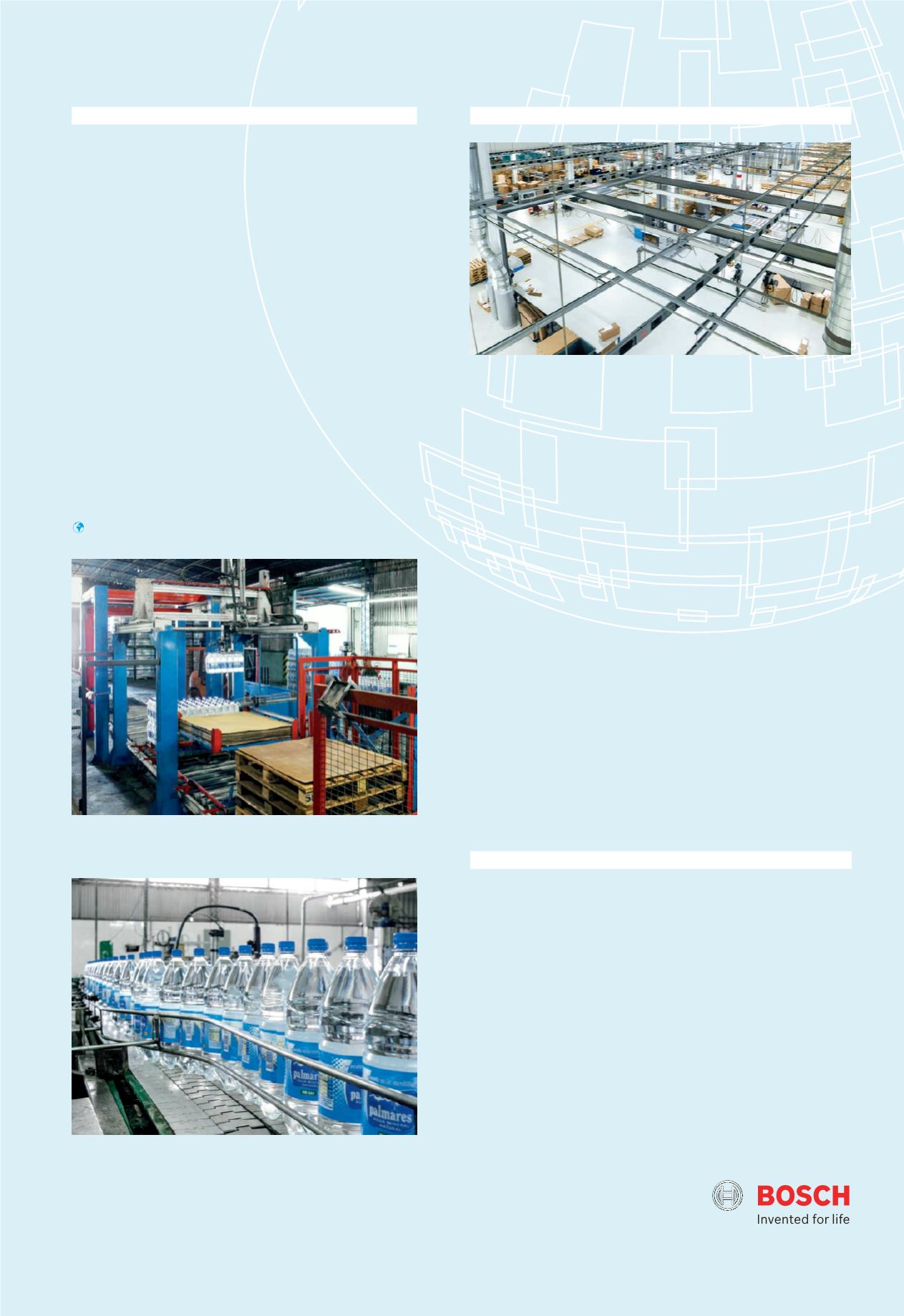
Issue 28
trends in automation
Festo worldwide
35
–
36
A lot of bottle
Efficient process for bottling drinks
Palletising,
which used to be the manual bottleneck of the system,
has now been fully automated thanks to Festo components.
The new palletising system from Gaudium used at a drinks
filling plant in San Juan in western Argentina handles
5,200 bottles per hour. Palletising the bottle packs is the
last stage of the PET bottle production process. The process
used to involve a lot of manual work. By changing the plant
layout and using Festo components, the cycle time was
shortened and the process was made more efficient. It is
now possible to switch between up to eight different
formats, depending on the bottle shape and the
arrangement of the packs on the pallet.
The plant contains numerous technical solutions,
including classic pneumatic drives for linear movement
and rotation, electric drives for positioning, toothed belt
axes as well as magnetic, inductive and optical sensors.
Valve terminals are used to control the processes.
www.grupogaudium.com.arArgentina
Germany/International
Awarding performance
Festo as a Bosch Preferred Supplier
The Bosch group, high-tech company and the world’s largest
supplier to the automotive industry, has chosen Festo as a
preferred supplier of pneumatic technology. Festo has received
the Preferred Supplier status for above average performance in
collaboration with the Bosch group. The supplier evaluation
criteria includes strong delivery reliability, advanced technical
solutions, fulfillment of international standards and global
orientation.
Bosch honours its best suppliers each year with the Preferred
Supplier status. The Preferred Supplier status is valid worldwide
for all Bosch plants and all business
divisions.
USA
From New York to Ohio
New Regional US Service Centre is opened
The new Regional Service Centre (RSC) in Mason, Ohio, has
9,000 square metres of logistics space, a manufacturing area of
7,000 square metres and 2,600 square metres of office space.
The site in Mason sets new standards in the areas of automated
stock management, software technology and product
configuration. The automated distribution system will enable
even very large order volumes to be processed efficiently. The
high technical standards and optimised processes guarantee
fast and reliable delivery to customers. The location was chosen
for its good infrastructure thanks to numerous highway links,
several airports in the region as well as distribution centres for
large shipping providers.
Hauppauge will remain the corporate head office in the United
States. As well as the Sales, Customer Service, Engineering,
Marketing, Finance and IT areas, Prototype Development and
Assembly as well as current Process Automation projects will
remain in Hauppauge.
Up to 5,200 bottles
per hour are handled by the
new palletising system from Gaudium.
Modern workplace:
in the manual packaging area, Festo products are
packaged according to customer specifications and prepared for delivery.