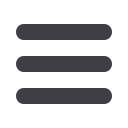
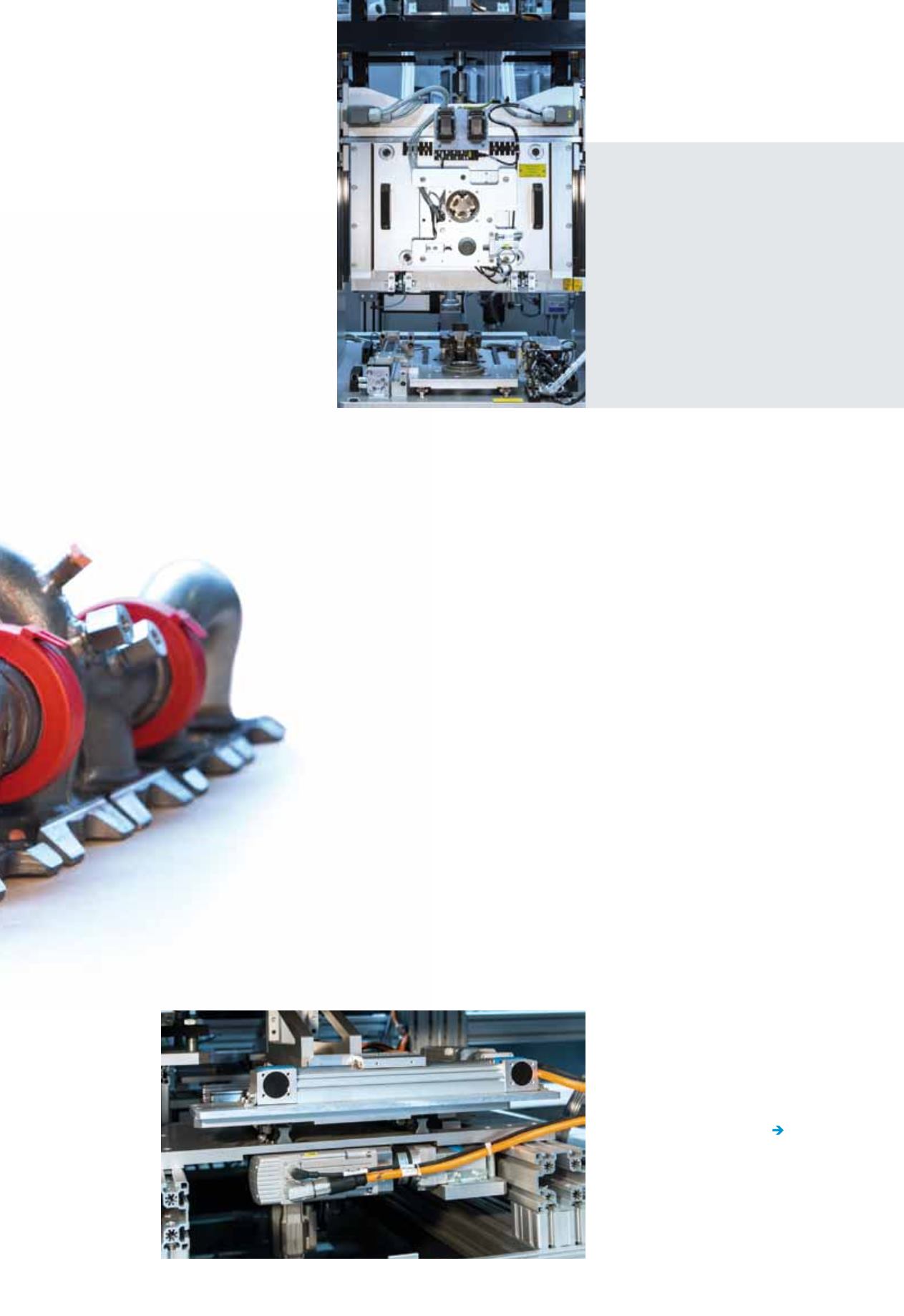
Speed up production
Bei der Endmontage auf der neuesten Fer-
tigungslinie setzte Bosch Mahle Turbo
Systems auf maschinenbauliches Know-
how aus der Umgebung – als Partner hol-
te man J&M Maschinenbau aus dem nur
wenige Kilometer entfernten Bleiburg ins
Boot. Dabei war Tempo gefragt, denn
Bosch Mahle Turbo Systems wollte einen
„Turbo für die Turbofertigung“.
Dipl.-Ing. Ferdinand Hochhauser, Ge-
schäftsführer Bosch Mahle Turbo Sys-
tems: „Bei der Endmontage werden über
30 Einzelteile auf unterschiedlichste Art
und Weise zu einem Turbolader zusam-
mengefügt – aufnehmen, zuführen, einle-
gen, verpressen, verschrauben oder mit
einer Schelle fixieren und das in wech-
selnden Positionen. Zudem wollten wir
verschiedenste Typen auf der Linie ferti-
gen können – ohne tagelange, teure Um-
bauten an der Maschine vornehmen zu
müssen. Das Zellenkonzept mit den
durchdachten Umbausätzen von J&M hat
uns da überzeugt. Wir sparen damit hun-
derttausende Euros schon bei der An-
schaffung jeder einzelnen Fertigungszelle
und wertvolle Zeit beim Umrüsten.“
Modulare Anlage
Die Endmontage verfügt gegenwärtig über
vier Zellen – es können aber auch typenab-
hängig mehr oder weniger sein. Dank der
modularen Lösung von J&M kein Problem:
„Wir beschicken die nebeneinander be-
findlichen mobilen Zellen mit einem Robo-
ter, der den entstehenden Turbo einer Be-
arbeitungszelle nach der anderen zuführt.
Ändert sich die zu fertigende Type, wird
einfach eine Zelle oder ein Teil von ihr ent-
fernt und eine andere Zelle oder ein Um-
bausatz eingefügt. Sind nur drei Zellen er-
forderlich, lässt der Roboter eine Zelle aus.
So sind wir hoch flexibel und unser Kunde
erspart sich Zeit, Geld und braucht gegen-
über älteren, ähnlichen Anlagen um einen
Werker weniger“, erklärt Albin Jelen, Ge-
schäftsführer von J&M Maschinenbau.
Verdichtergehäusemontage
Viele Bearbeitungsschritte sind notwen-
dig, bis der Turbo die Endmontage in Rich-
tung des finalen Schweißvorgangs ver-
lässt. Den Auftakt bildet Station 1 – die
Verdichtergehäusemontage. Der Roboter
übernimmt die vorgefertigte Rumpfgrup-
pe aus dem Arbeitsfluss und legt sie an
der Rückseite in die Zelle ein. Dann wird
der Tisch mithilfe von zwei pneumati-
schen DGC-Achsen nach vorne in den Ar-
beitsbereich der Station geführt. Dort hält
ein Dreipunktgreifer HGDT das manuell
eingelegte Verdichtergehäuse von hinten
fest. Anschließend schwenken DSBC-Zy-
linder die gesamte Haltevorrichtung mit
dem Greifer und dem Gehäuse um 90
Grad, um die Rumpfgruppe sanft von
oben anpressen zu können.
Der Turbolader
– unerlässlich
für Höchstleistungen und Effizienz
bei Kolbenmotoren.
In Station 1
sorgen
Pneumatik und Elektrik
von Festo für die Montage
des Verdichtergehäuses
auf der Rumpfgruppe.
Zwei EGC-Achsen
mit Festo Servomotoren
EMMS positionieren den x/y-Tisch mit dem
Schrauber im unteren Bereich von Station 1.
Bilder: Martina Draper
3.2015
trends in automation
Synergien
34
–
35