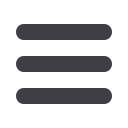
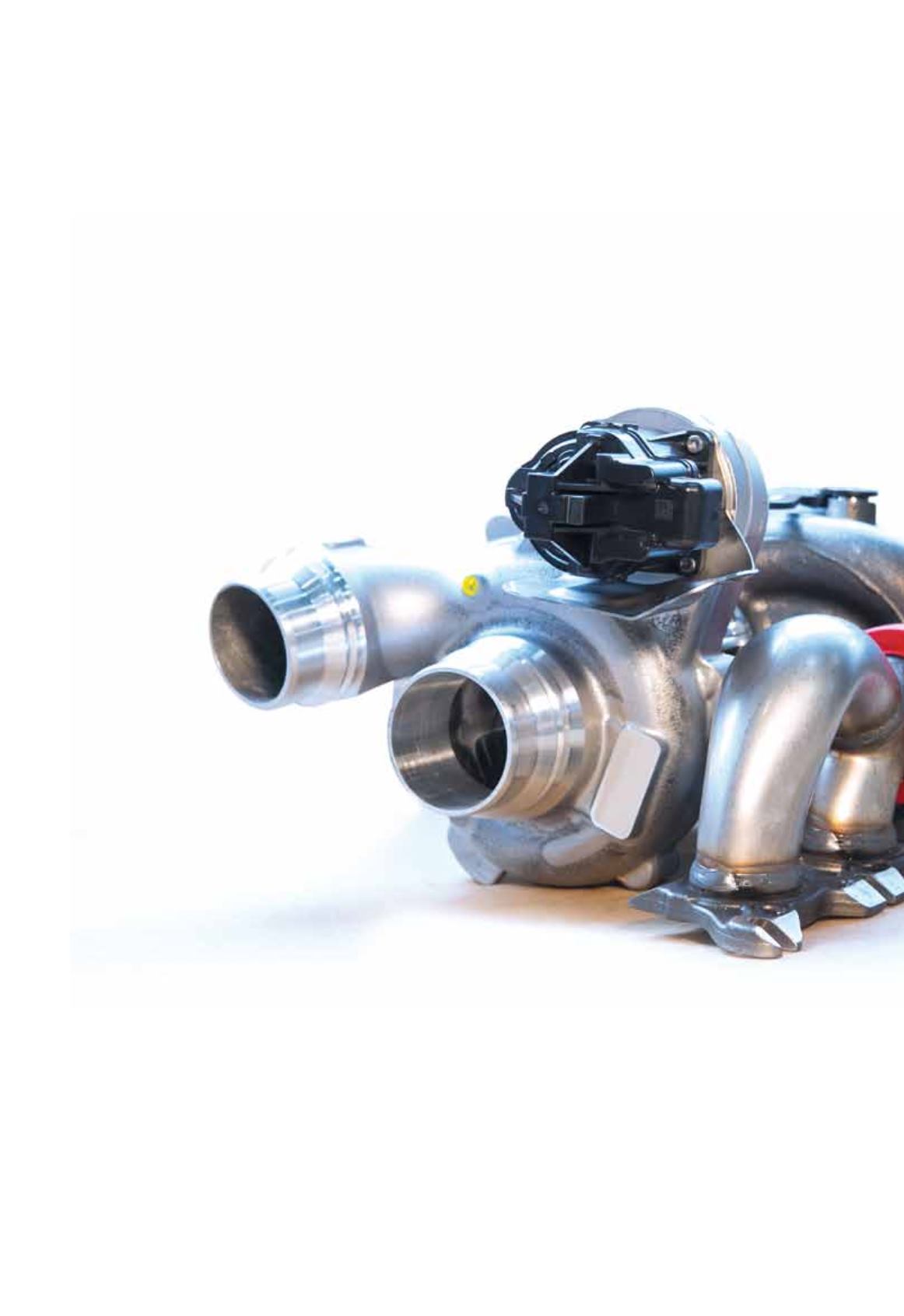
Z
urücklehnen, Gas geben und spü-
ren wie der Wagen die Kraft zuver-
lässig auf die Straße bringt. Auch
wenn man kein Raser ist – Dreh-
moment und „Pferdestärken“ sind
Trumpf. Und das bei möglichst kleinen
Motoren, denn so spart man Bauraum,
Gewicht, Kosten und natürlich Sprit. Tur-
bolader sind daher heute nicht mehr weg-
zudenken – sie sorgen für höchste Leis-
tung und Effizienz bei Kolbenmotoren.
Dabei ist ihre Arbeitsweise ebenso inter-
essant wie wirkungsvoll: Die Abgase des
Motors werden über eine Turbine ge-
führt, die wiederum über eine Welle ei-
nen Verdichter antreibt, der die Ansaug-
luft des Motors vorkomprimiert und so
für einen höheren Druck im Zylinder
sorgt. Zusätzlich wird bei modernen
Fahrzeugen die Ansaugluft nach dem
Verdichten durch einen Ladeluftkühler
gekühlt, um eine noch größere Dichte
mit mehr Sauerstoff und damit einen
besseren Wirkungsgrad des Motors bei
der Verbrennung zu erreichen.
Über 100 Jahre Entwicklung
Das Prinzip des „Turboladers“ kennt man
schon seit über 100 Jahren, denn die
Grundlage legte der Schweizer Alfred Bü-
chi, der schon im Jahr 1905 ein Patent für
die Gleichdruck- bzw. die Stauaufladung
anmeldete. Erste Straßenfahrzeuge mit
Turboladern wurden ab den 1930er-Jahren
produziert.
Seither hat sich viel getan in Sachen Tur-
bo-Optimierung, was sich in der hoch-
komplexen Fertigung der aus vielen Kom-
ponenten bestehenden Turbolader
widerspiegelt. Das ist die Spezialität der
im kärntnerischen St. Michael beheima-
teten Firma Bosch Mahle Turbo Systems,
die die Autoindustrie weltweit mit unter-
schiedlichsten Turboladern versorgt.
Ein Turbo für
die Turbofertigung
Automobilindustrie
Turbolader verhelfen Kolbenmotoren zur Höchstform
–
Effizienz und Tempo sind gefragt. Das gilt nicht nur für das
Fortkommen auf der Straße, auch bei der Fertigung des
Turbos selbst wird ganz genau auf die Uhr geschaut.
J&M Maschinenbau sorgt mit Elektrik und
Pneumatik von Festo für „Fullspeed“ bei
Bosch Mahle Turbo Systems.